Result Summary
The fatigue failure initiated on the outside bottom where the carafe had been scratched with the abrasive scrub pad. As a result of cyclical thermal shock (between 195°C and 15°C), the cracks grew progressively till it reached a critical length. Glass thickness at the origins is approximately 3 mm. One failed after 12.
Introduction
In order to simulate normal, use, coffee carafes were scratched with a chosen abrasive and thermal cycled. In this case a commercial scrub pad was used. It is a sponge with embedded 320-400 grit aluminum oxide. This scratching is to simulate both cleaning and sliding the carafe on hard counter tops. In this test, the bottom of a new borosilicate coffee carafe was scrubbed with a wet abrasive sponge and then thermal cycled numerous times till a visible crack formed. A carafe that failed after 51 cycles is examined. The progressive crack initiated at an abrasive scratch.
Results
51 Cycle Failure
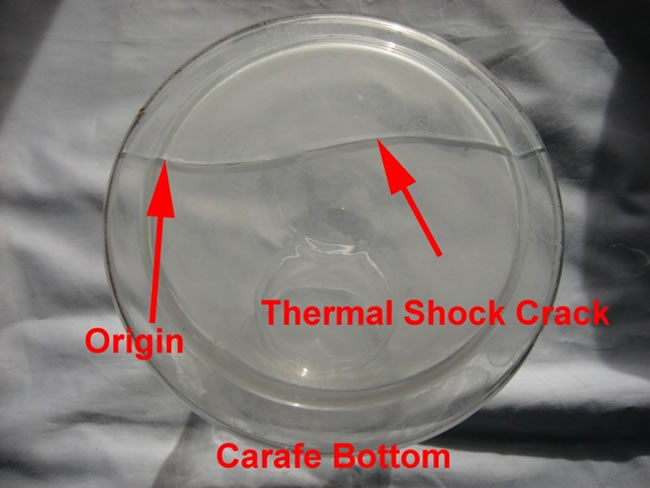
Figure #1: Photograph of the failed carafe bottom. The “wavy” nature of the crack indicates that it was driven by thermally generated stress.
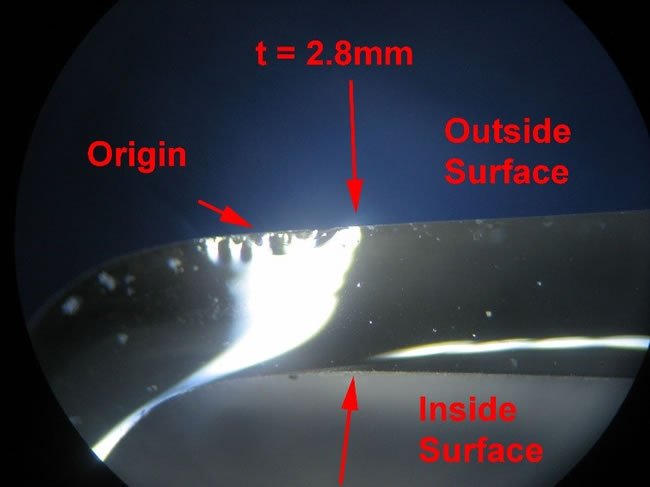
Figure #2: Photomicrograph of the fracture origin on the fracture surface. The fracture originated at an abrasive scratch. As a result of thermal shock, the crack grew progressively till it reached a critical length. Glass thickness at the failure origin 2.8mm (Mag. 10X).
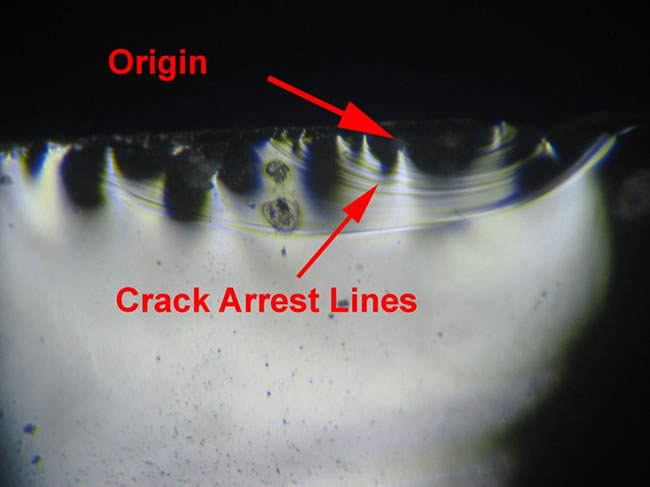
Figure #3: Higher power photomicrograph of the fracture origin on the fracture surface. The crack initiates on the outside bottom where the carafe had been scratched with the abrasive scrub pad. As a result of stresses from thermal shock, the crack grew progressively till it reached a critical length. Glass thickness at the origin 2.8mm (Mag. 40X.
Dr. Thomas L. Read, CEO of Read Consulting received his PhD. from Stanford University in 1972. He has over 25 years of manufacturing experience in electronics, metallurgy, factory safety, failure analysis, glass fracture, glass failure and bottle failure. As a member of the electronics industry, Dr. Read has earned process patents and has an extensive background in manufacturing techniques. In parallel, he has spent over twenty five years as a consultant to attorneys and engineers in the areas of failure analysis, metallurgy, glass fracture, glass failure, bottle failure, factory safety, manufacturing problems, intellectual property and patent disputes.
©Copyright - All Rights Reserved
DO NOT REPRODUCE WITHOUT WRITTEN PERMISSION BY AUTHOR.